Productivity and efficiency are core elements of any high-performing business. KPIs like SoW and downtime within a large volume, automotive production line are critical to its successful operation. Why? Because time really is money.
That said, to reach the pinnacle of productivity requires a holistic approach. In today’s world of automation and Industry 4.0, digital technology is providing new ways to make sure that your team are working effectively and that your machinery is calibrated for the job. But even when machine settings have been optimised and the material is within specification, production can still be derailed by variation in properties of the input material and pressing process.
In the context of an automotive press shop, you need a steel that delivers the same results time after time. Tata Steel’s high-strength, highly formable DP800 steel benefits from consistent and stable mechanical properties, thanks to the tight manufacturing controls which provide tightly controlled mechanical properties, a uniform surface quality, exceptional flatness and tight gauge tolerances, creating a steel that is more consistent than any specification dictates.
Using Tata Steel’s DP800 has multiple benefits for press shops seeking to improve their productivity. First and foremost is the ability to save time. A dependable, reliable and repeatable product requires little intervention from the quality team. If things do go wrong, there is support from Tata Steel's experts to provide help to obtain a long term solution. Think of the wasted time involved in stamping parts from a product that varies in properties like strength along the coil or from blank to blank resulting in higher reject rates and reduced productivity. It can have major implications on costs, as well as deliverables for you, your customers and the end user.
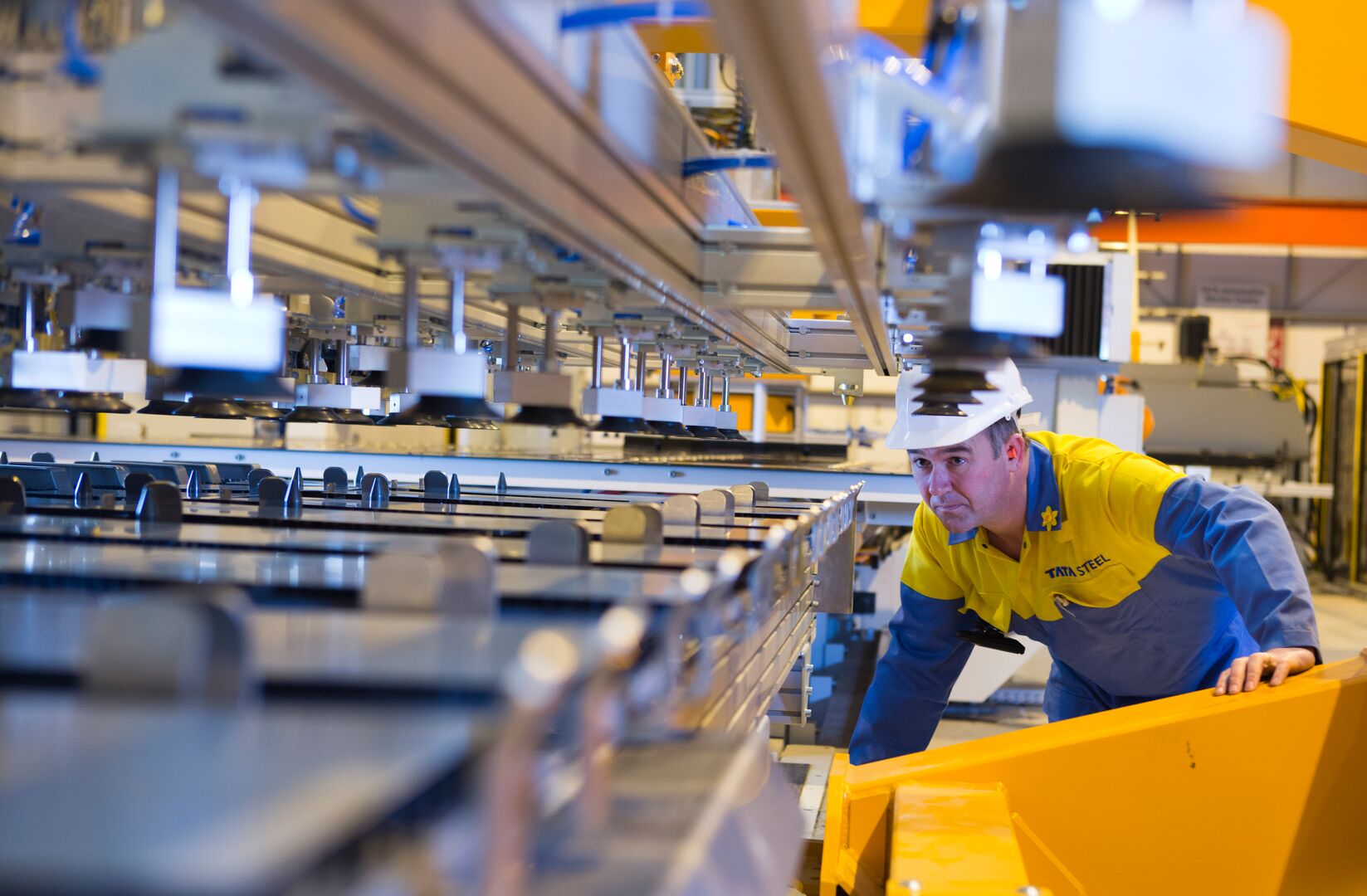
Conversely, highly consistent material has the capability to help save time. The stability of DP800, as well as its leading formability characteristics, leads to fewer splitting issues. As such, you enjoy less downtime and higher productivity.
Another consideration is the manufacturing process window requirement for DP800 during stamping process design. A greater coil-to-coil consistency means that a more robust process is easier to design, enabling the production line to be in operation quickly and more reliably.
As we’ve addressed already, time savings go hand in hand with an increase in productivity and efficiency. But what about waste? Unused material is a cost and environmental burden on the manufacturing process and businesses are, naturally, always seeking ways to mitigate it. Once again, Tata Steel’s DP800 has a role to play in the process. Fewer manufacturing failures brought about by the steel’s chemistry and formability characteristics mean fewer discarded parts and a greater yield from the coil. Steel is also 100% recyclable so any trimmed off material can go back into making more DP800 or any other grade of steel.
Improving the efficiency of your manufacturing process need not be rocket science. While there are simple changes to be made, it’s vital that you review the journey as a whole. Ask yourself one question - could your steel be working harder for you?
Find out more about our range of advanced and ultra high-strength steels here.